Field Day is always an important event for the GCARC Skunkworks team. A single satellite QSO is worth 100 bonus points – more points than some single-band stations get throughout the entire contest – and everyone in the club knows whether we’ve succeeded or failed at getting that QSO. And the satellite station needs to be fully-functional – we need the best antennas that we can get along with an azimuth-elevation rotation system that will track satellites as they move across the sky. During Field Day satellite signals are far weaker than at other times because the power budget of the satellite is fixed and gets distributed among all stations. Normally when only a few stations are using a satellite each station gets a significant portion of that budget with a commensurate signal strength level, but on Field Day a dozen stations may be vying for those watts with a resulting decrease in the level of each signal.
In earlier years we used the “Armstrong” method of antenna rotation with volunteers aiming the Arrow portable antennas at the satellite, and although we were always successful at making at least one contact this process was clearly suboptimal. Last year we had obtained the M2 “LEO Pack” of crossed yagi antennas for 2 meters and 70 cm but using the Portable Rotation rotator (which has since been discontinued) didn’t work very well – it had a tendency to wrap the feedlines around the mast if not carefully supervised during a pass, and it also seemed to lose calibration easily.
This year Frank N3PUU decided to build the V3 az/el rotator developed by the SatNOGS team that also manages the satellite telemetry tracking network. This uses stepper motors as the basic motor and creates antenna rotation through a large set of 3D printed gears. Over the past year Frank printed and assembled the rotator and he, John K2QA and I took it down to the GCARC Clubhouse for testing a couple of weeks before Field Day.
Those tests were disappointing. While the azimuth rotator was able to rotate the antenna array around the horizontal axis the elevation rotator didn’t have enough torque to elevate the antennas. At that point the antennas hadn’t been balanced – each was mounted at the recommended mounting point that created more weight on the front of the antenna array than on the back. Additional technical issues occurred at that point so we had to abandon that effort with Frank planning to do additional testing to ascertain the problem with the elevation rotation.
The following Saturday we reconvened, Frank having checked all of the motors and other components and verifying that they worked properly. It appears that the SatNOGS design didn’t provide for motors having enough torque to rotate the complete LEO Pack antenna setup. However, we still believed that with proper balancing of antennas we could still get the elevation rotator to work, and we were finally successful after tying the feedlines back up the antenna masts to the boom, remounting both antennas closer to the balance point and adding some small weights by tie-wrapping washers to the end of the antenna. All of this may have affected the RF pattern but it was necessary to make the elevation rotator functional. We did find that the rotator would lock up when rotating at about 80 degrees of elevation (which is strange because higher elevations should require less motor torque) which we solved by locking the maximum elevation in the PST Rotator controller program at 75 degrees. This solved the rotation issue.
We also had experienced interference on the 70 cm downlink frequency from the 2 meter uplink signal (satellite operation is cross-band and full-duplex). This was solved with a diplexer that split the 2 meter and 70 cm signals and fed the 2 meter signal into a dummy load while passing the 70 cm signal through to the receiver. We used a SDR Play radio and the SDR Console program for the downlink and an IC-7100 for the uplink.
Other important station components were a multi-port headphone amplifier that allowed multiple operators to listen to the received signal and vary their own volume levels – this was especially critical because of a large noisy event occurring in the field next to the Clubhouse. A secondary display on my Dell laptop allowed viewing the PST Rotator screens showing the satellite and rotator positioning as well as upcoming satellite passes on one screen with the SDR display on the other. My Honda 2200 inverter generator loafed along providing power for the weekend.
Greg W5DO and I made a few test contacts before the 2 PM Field Day start time to be sure that everything was working. Once the event started we had to wait until the next satellite pass and in the second group of passes around 5 PM we made our “bonus” contact on AO-7, the oldest of the ham radio satellites still in operation. After that we tried working several other passes but found that the FT-8 station on 6 meters would clobber our reception at unpredictable times. We also found that signal strength was quite weak – much weaker than we found at the Clubhouse satellite station during the same period. This made us suspect that the RG-58 feedline that we were using was the cause, so a goal for next year is to either replace that feedline or install a preamp near the antenna. These issues combined together caused us to conclude that getting the first bonus contact was worth the effort but getting additional contacts was not, so we shut down the satellite station around 9 PM.
Overall the project was a success – we maintained our record of getting the satellite bonus contact each year that we attempted it, and had no major hardware or operating failures once we got everything working. Our goal for next year will be to improve the receive signal strength to make contacts easier, and to continue our previous successes.
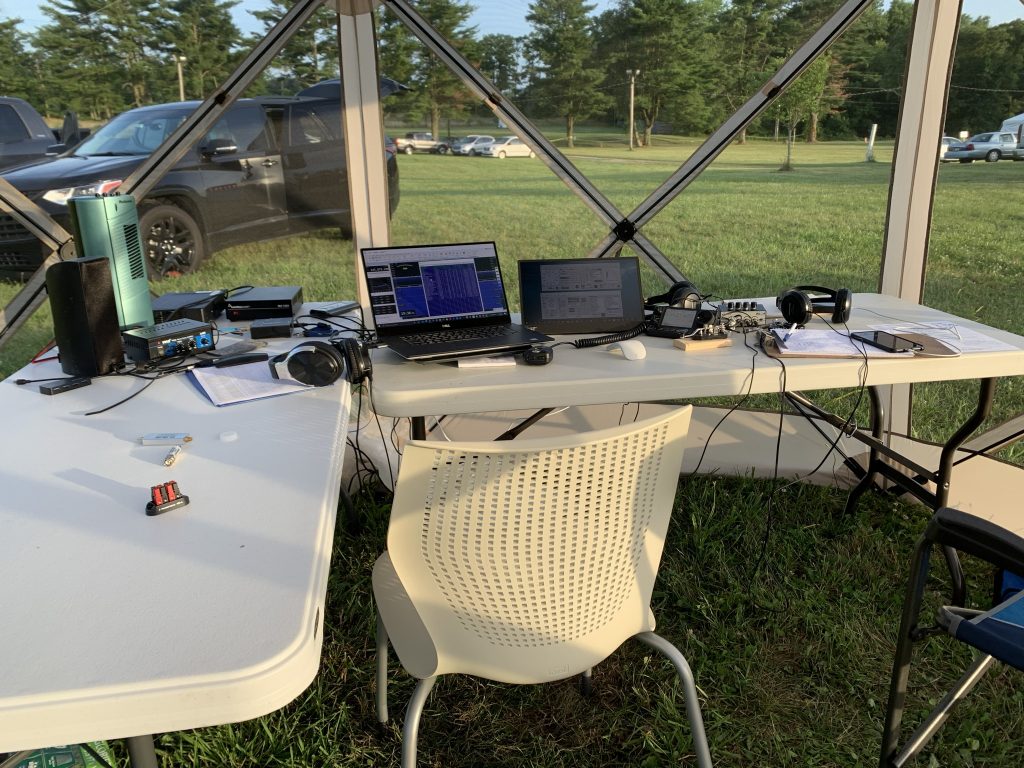
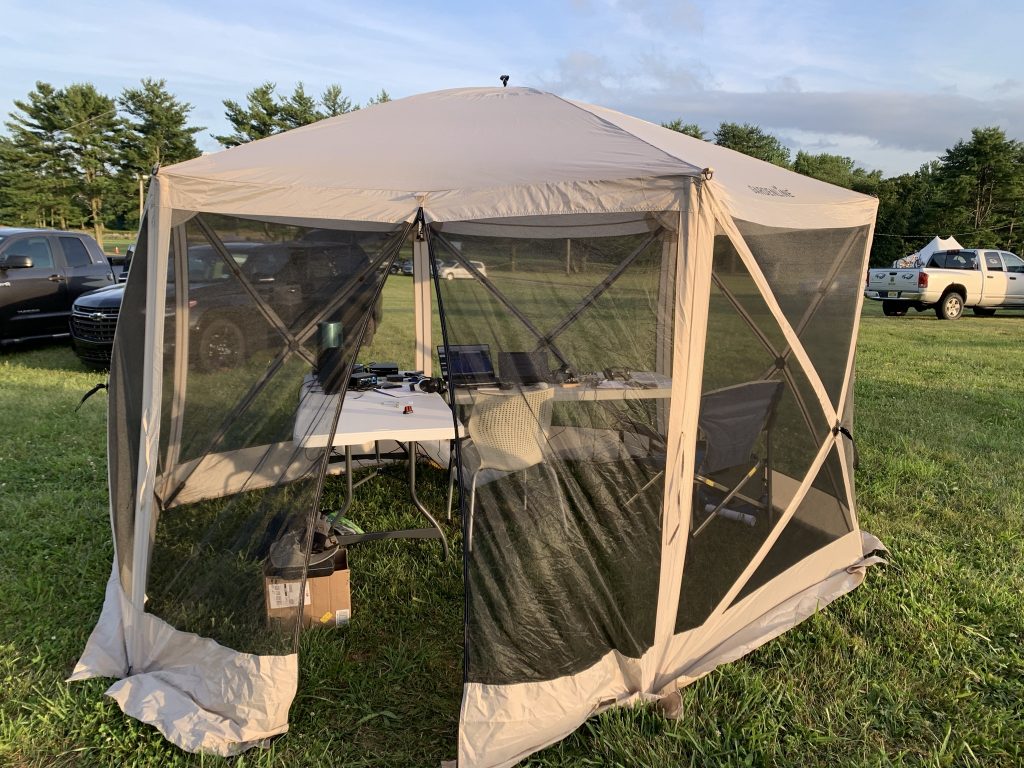
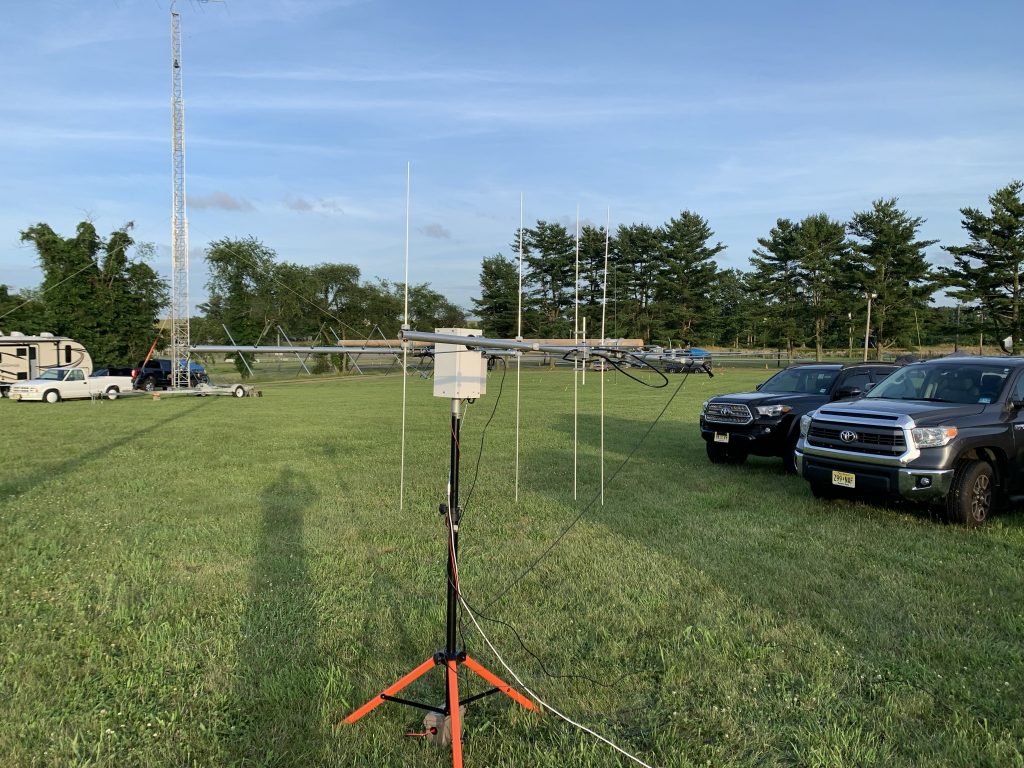
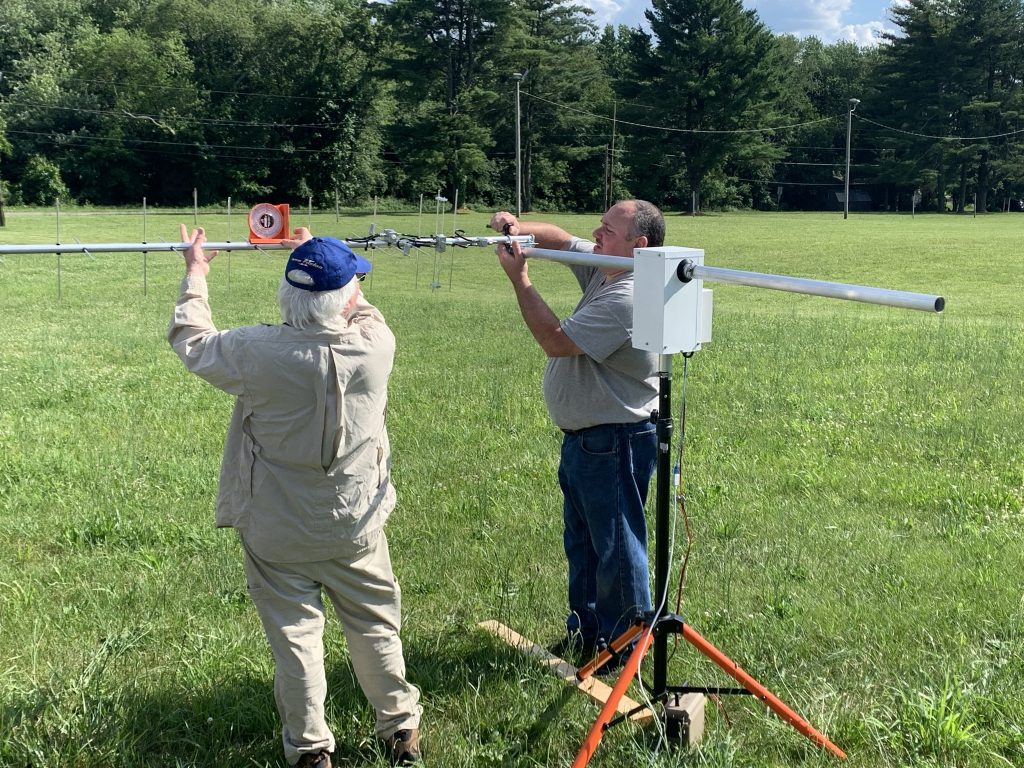